In the standard concentrator plant geometallurgical modeling process, the comminution and flotation stages are often modeled separately. However, this approach does not allow the joint behavior to be easily quantified.
A better course of action considers the integration of both stages of the process; the challenge is to create a meaningful link between both circuits. This can be achieved, for example, by expressing the flotation behavior as a function of the feed particle size and the retention time.
To meet this objective, there are several modeling alternatives on the market with different degrees of complexity; however, the cost and time it takes to calibrate these models tends to be high when it comes to project long-term production.
A standard tests program for geometallurgical purposes considers comminution rates to build throughput models, rougher flotation tests (collecting partial concentrates) to estimate kinetic parameters, and locked cycle tests to obtain cleaning efficiencies. Finally, the effect of the size of the primary grind on the metallurgical performance is studied in a subset of samples.
The flotation stage is integrated into the comminution stage by parameterizing the flotation kinetics as a function of the ball milling product particle size. These algorithms are implemented in the geometallurgical block model and allow mapping the expected behavior of the comminution-flotation circuit in each zone of the deposit.
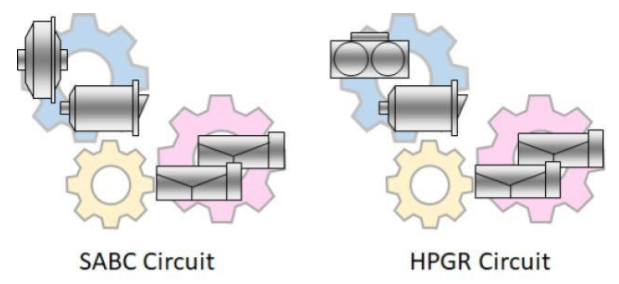
Through this methodology it is possible to study changes in the configuration or operating conditions of both stages effectively. Thus, sensitizing effects on processing capacity, rougher retention times, recoveries and concentrate grades.
At Mine to Port Consulting, we have developed various integrated models for (SABC / HPGR) – flotation circuits, customized according to the needs and challenges of our clients.
Do you want to implement these models in your project? Let’s talk, mail us to contacto@m2p.cl